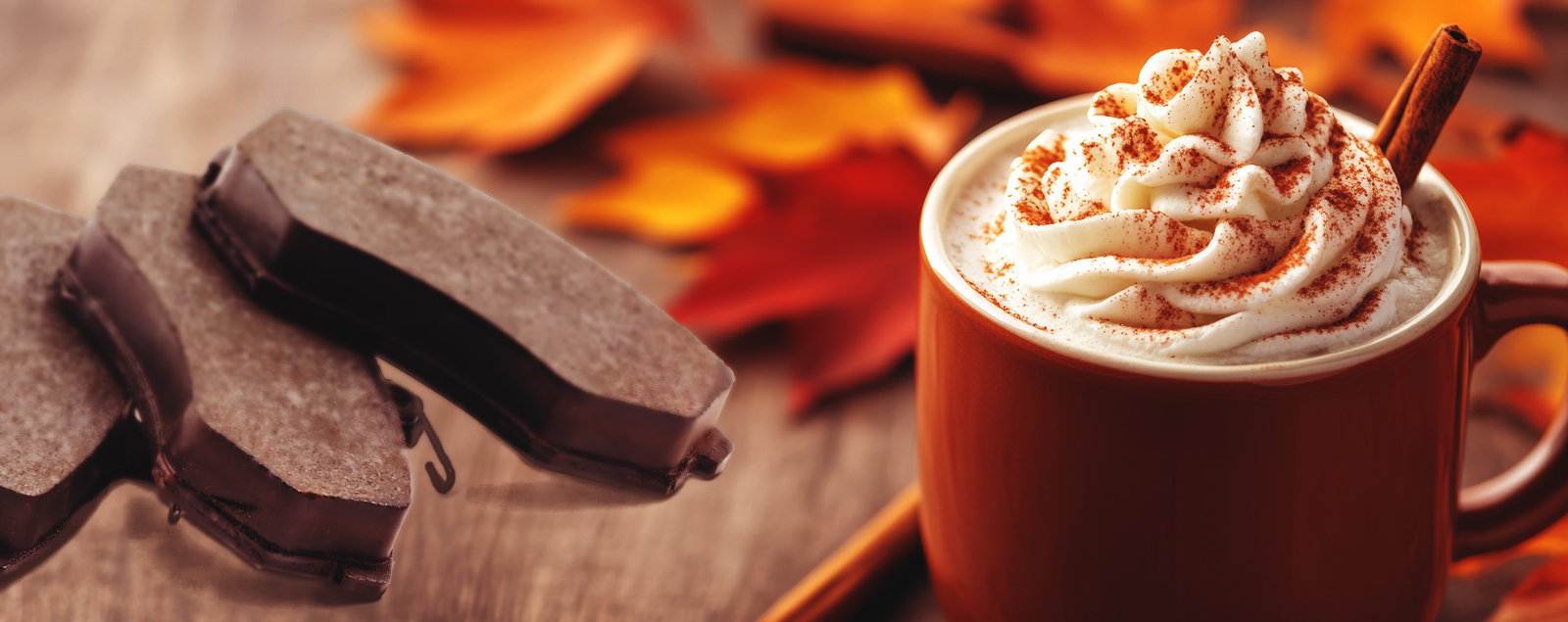
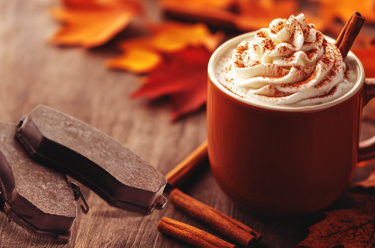
The importance of winterizing brake systems
Any time of year is right for brake system maintenance, but colder weather poses some special challenges for technicians. Key brake components are stressed by cold, moisture, and the salt that some locales use to deal with snow and ice. Added issues come from reduced driving during severe weather, resulting in cars sitting days without driving. Rust never sleeps even when the car is napping.
Winter weather affects each brake component differently and servicing each component requires specialized knowledge. Each manufacturer may have unique procedures to follow and having complete OEM service information is critical to your customer’s safety and your shop’s reputation.
Brake Pads
Pads that may have material beyond the minimum thickness can still be candidates for replacement. A thorough inspection of the pads and all related brake components is needed.
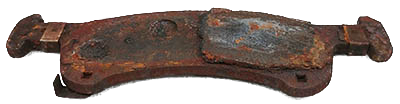
These are items that technicians should be on the lookout for:
- Corrosion may be present between the friction material and the steel backing plate. This may cause the friction material to break free from the backing plate causing loss of stopping power.
- There may be heat cracks present in the friction material which may result in chunks of the friction material falling off.
- Anti-rattle shims and wear indicators may have rusted away.
Brake Rotors
There was a time when brake rotors had a cast-in hub configured for tapered roller bearings. These rotors were big, heavy and expensive. They were often “turned” on an off-car lathe to ensure they were within tolerances for run-out and parallelism while remaining above minimum thickness.
Because they were heavy and thick, they didn’t chatter during machining and the results were usually good.
As the market moved to front-wheel drive and manufacturers embarked on a crusade to shed weight, the hubless (hat-style) rotor began to dominate the landscape. Being light, they were a bit more difficult to machine well off-car; on-car lathes became more popular.
Being light and thin, the hubless rotors didn’t have a lot of material that could be removed before reaching minimum thickness. Additionally, due to market dynamics, the price of new rotors fell, and the labor rate went up. The brake lathe soon gathered dust in many shops: replacing rotors was cheaper.
Some manufacturers (mostly European) see the rotors as parts that wear at about the same rate as the pads. In those cases, rotor and pad replacement is done simultaneously.
On any vehicle, the rotors do exchange material with the pads and replacing them as a set is often a good idea.
If rotors are replaced, clean the hubs of all rust and dirt. Failure to do so can introduce excessive runout on new rotors. If you have excessive run out on a new rotor (and the hub is clean), try removing the rotor and reinstalling it 180° from the initial position.
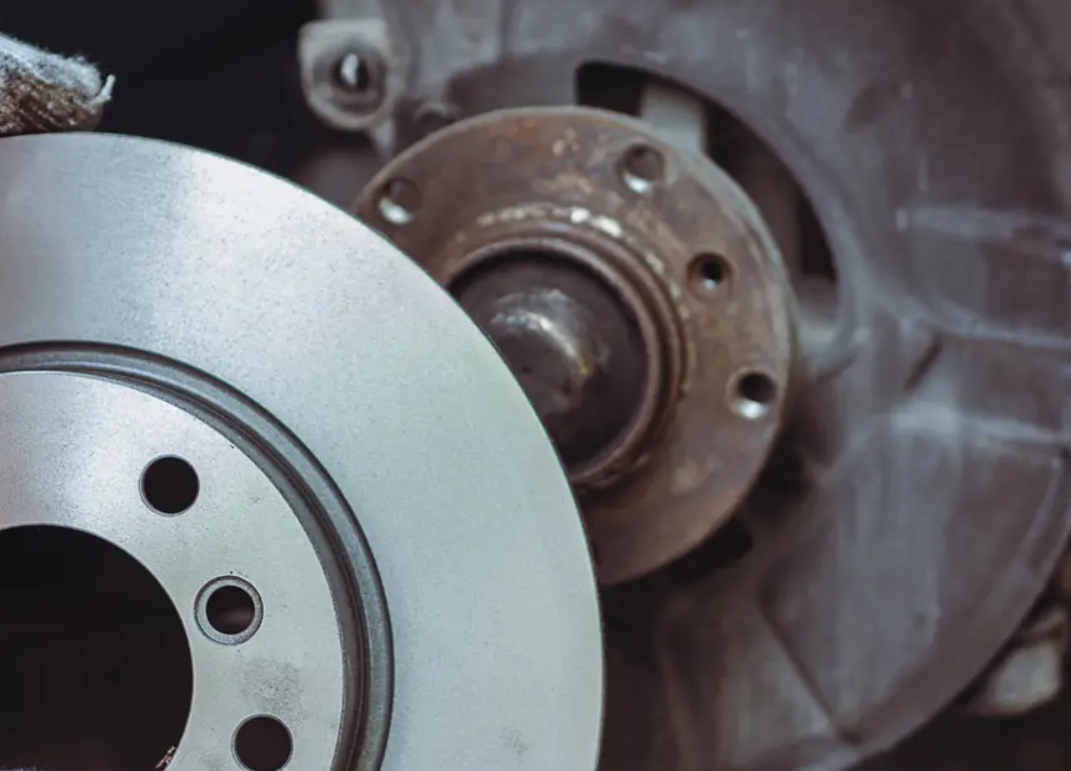
If the rotors are to be reused check the following measurements using a dial gauge and an outside micrometer. Compare to the manufacturer’s specifications:
Brake Disk Runout: | |
Service limit: | 0.04 mm (0.0016 in.) |
Brake Disk Thickness: | |
Standard: | |
NISSIN type: | 27.9-28.1 mm (1.10-1.11 in.) |
AKEBONO type: | 22.9-23.1 mm (0.90-0.91 in.) |
Max. Refinishing limit: | |
NISSIN type: | 26.0 mm (1..02 in.) |
AKEBONO type: | |
Brake Disc Parallelism: 0.015 mm (0.0006 in.) max. |
Runout
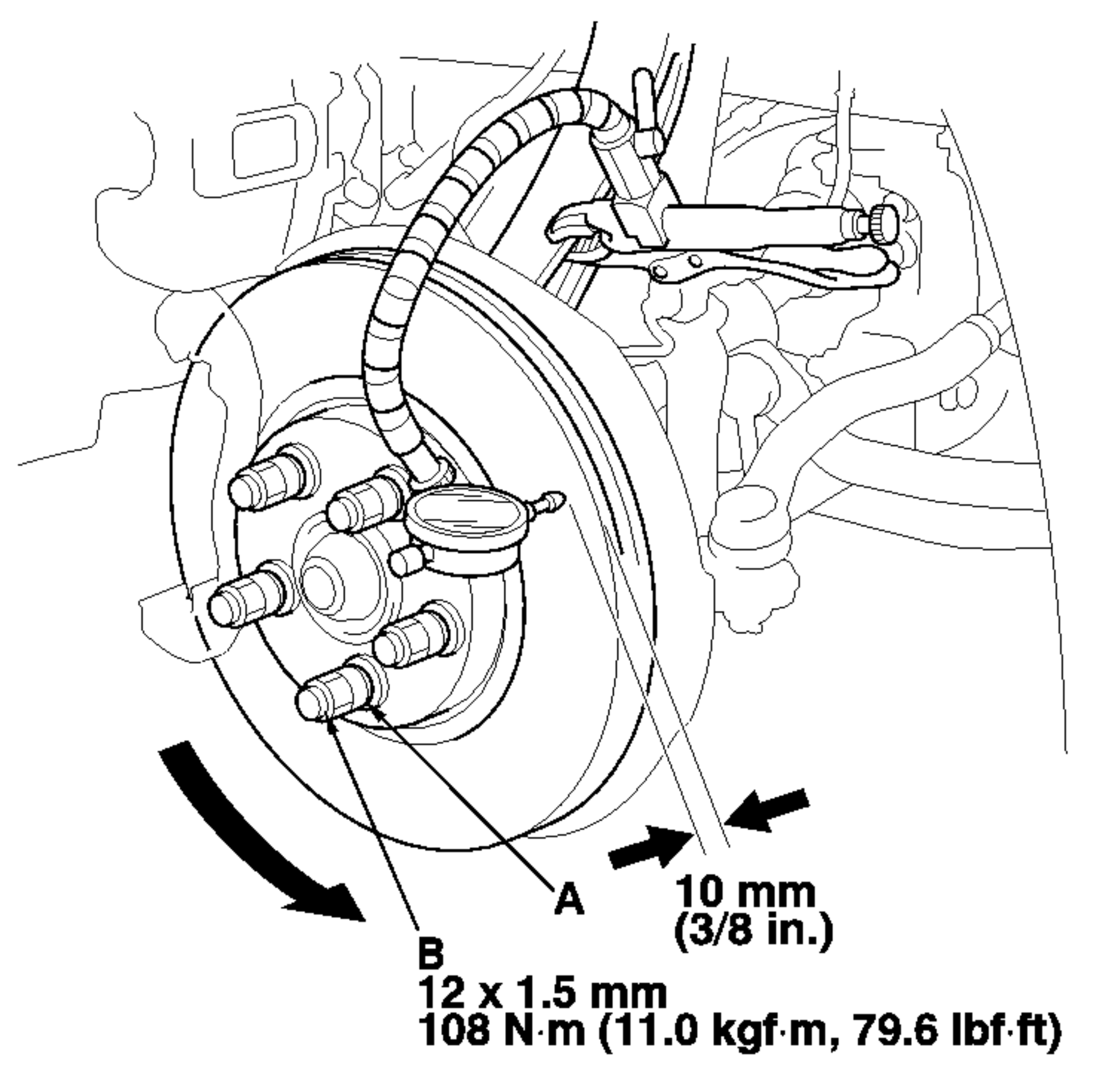
Parallelism (check in 8 places)
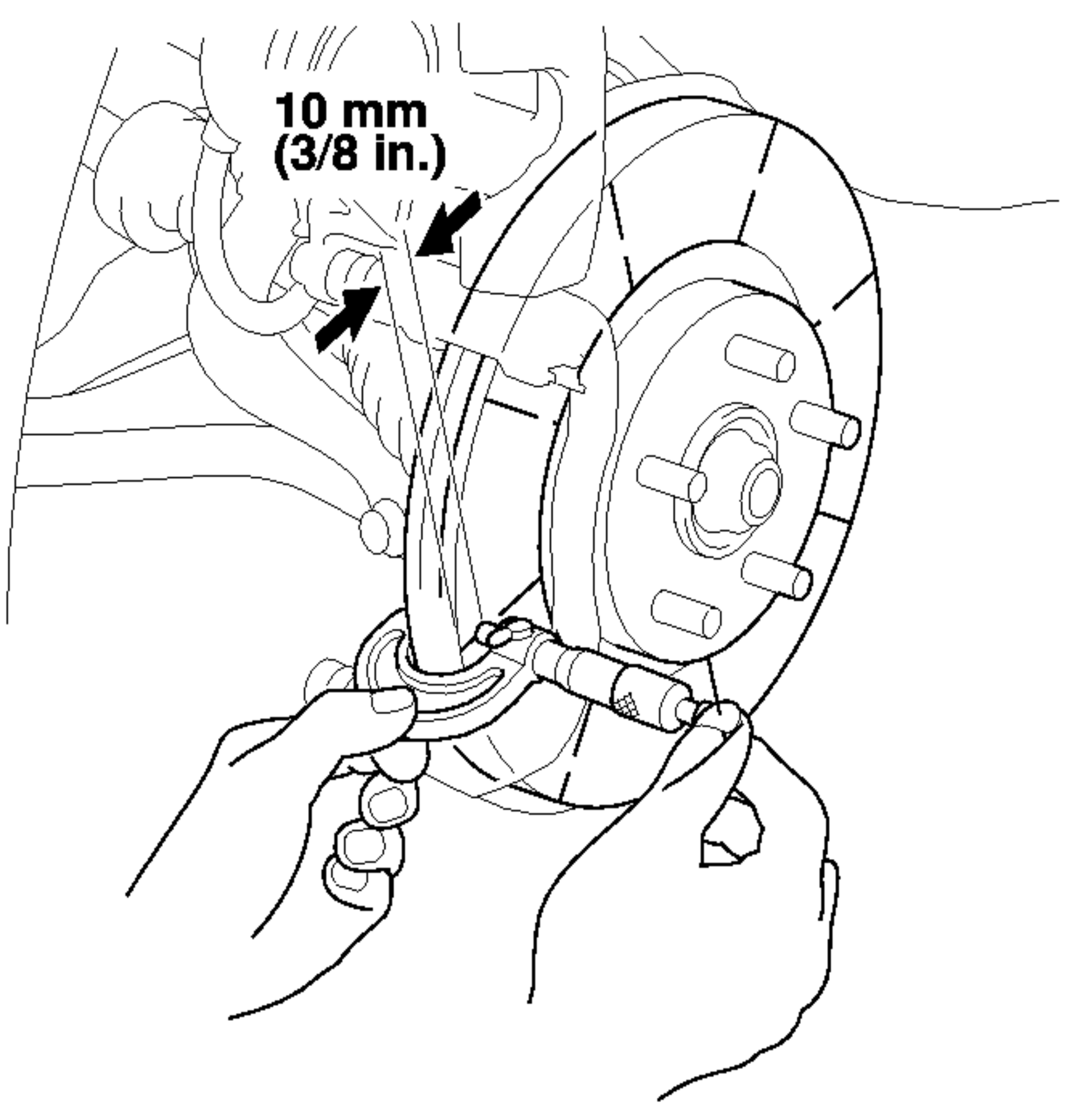
Brake Calipers
Calipers live in a hostile environment. They’re exposed to heat, salt, water, and even harsh soaps at the car wash. Often overlooked during a brake service, they can introduce many ill effects if they are not in optimum condition.
The term “pad slap” is sometimes heard regarding a “quick” brake service. In the haste, caliper guide pins are often ignored. The caliper guide pins on floating calipers should always be cleaned in solvent or replaced. The bores should only be cleaned with a nylon brush and solvent and new caliper-specific grease should be applied.
Replace any torn rubber slide-pin boots to keep moisture and other contaminants out. Failure to service the guide pins is the leading source of uneven pad wear. Customer complaints of noise will also result from binding guide pins.
Also, avoid using an impact wrench to remove or install the guide pins. Most guide pins are plated with an anti-corrosion material; spinning a guide pin in the bore could damage the plating.
Grab the small torque wrench and tighten the guide pin bolts to specification. Don’t overdo it, they have been known to break.
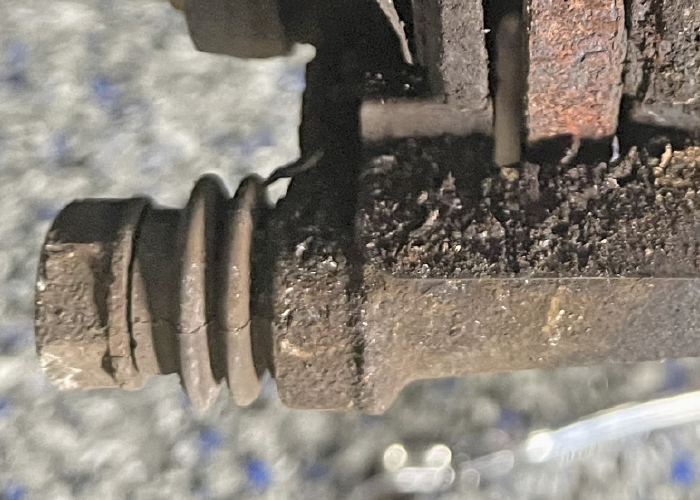
Caliper torque values and lubrication points
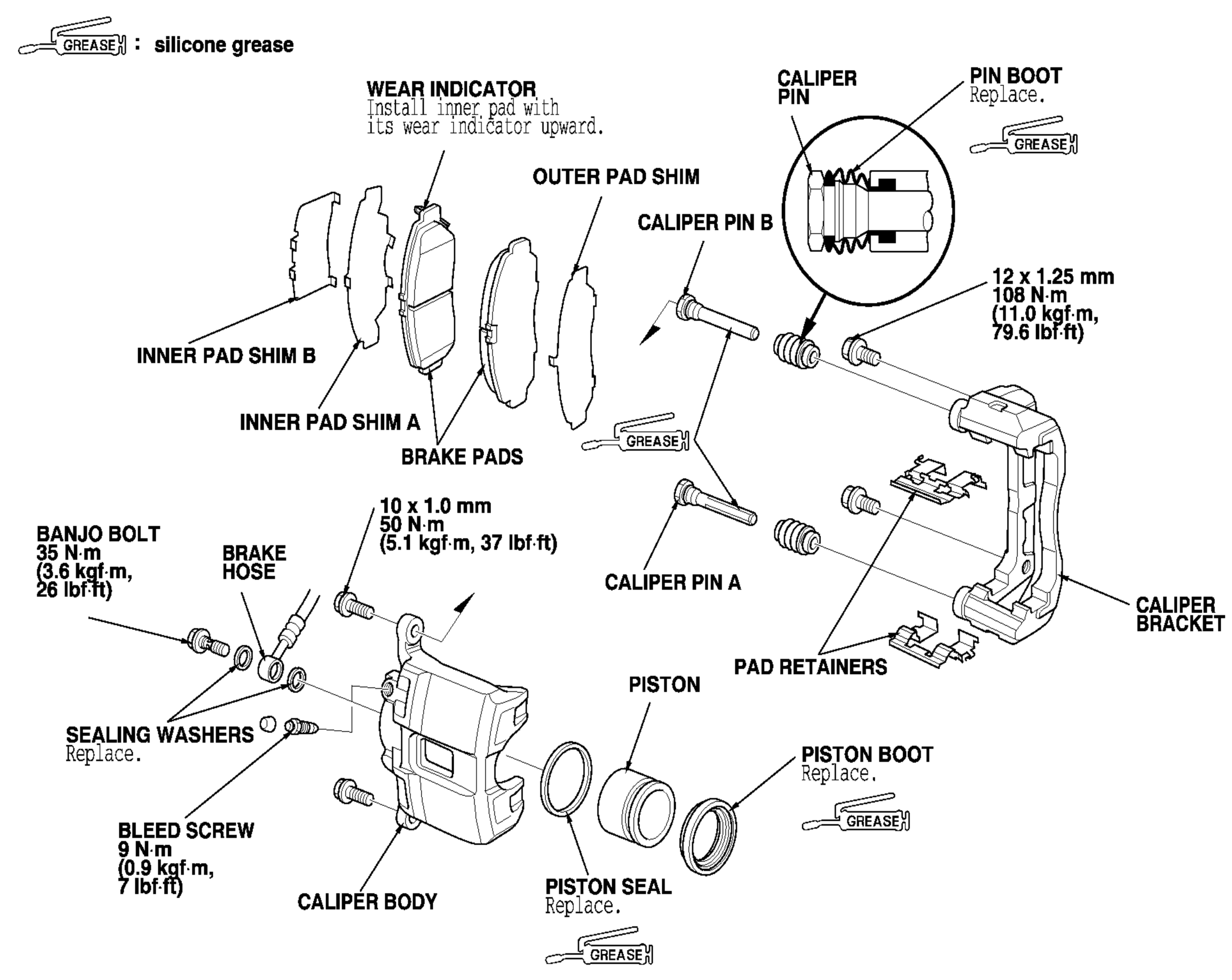
Brake Fluid
Brake fluid is often overlooked until major brake work is done. To give customers the highest level of service, check the brake fluid condition every time a vehicle enters your facility. At a minimum, the condition of the brake fluid should be tested every year, and the fluid changed if needed.
DOT 3 and DOT 4 brake fluids are hygroscopic - they absorb moisture from the air. Since the brake fluid reservoir must be vented to the atmosphere there is ample opportunity for the brake fluid to pick up a bit of water. This is normal and will happen anywhere but will occur faster in humid areas and during winter weather.
Is changing brake fluid considered scheduled maintenance?
That depends on the manufacturer. As an example, for the 2001 Honda Civic, it is recommended based on time or miles.
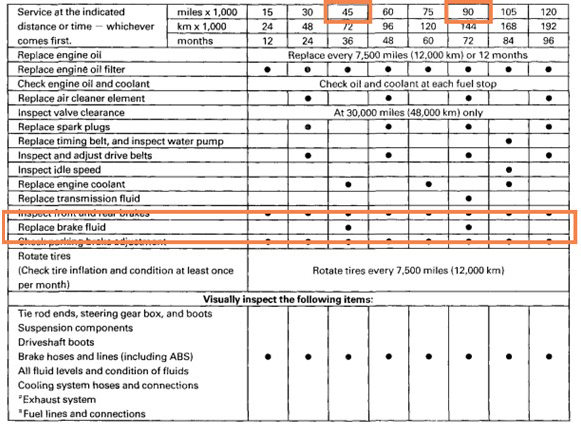
Testing methods
There are three commonly used brake fluid testing methods:
- Conductivity testing for water content
- Boiling point tester for water content
- Test Strips – some test for copper, some for moisture, some for ph
Which should you use? Ideally, all of them should be used.
Parking Brake
Another often ignored brake system is the parking brake. No matter if it is mechanical with cable actuators, or electronic with servo motor actuators, make sure it is in operating condition. The major enemy of a parking brake is a customer’s lack of use. Moisture works its way into the system and lack of use results in binding or lock-up due to the lubrication not being distributed by usage. There have been cases where a parking brake, once applied, refuses to release.
For safety and liability reasons, the parking brake operation should be inspected any time the vehicle enters a service facility.
Putting the Electronic Parking Brake (EPB) into service mode to retract the pistons will be necessary for any pad or rotor replacement on vehicles so equipped. This is typically accomplished with a scan tool or sometimes using buttons on the dash or steering wheel. The correct procedure will be found in the service information.
I’ll stop here…
The takeaways from this article: don’t ignore the condition of every component of the brake system. Incorporate proper brake service into your shop service operations. Consider replacing rotors as opposed to machining them. Caliper slide pins need attention on every brake pad replacement. Look for the effects of corrosion and heat. If the vehicle manufacturer has a stated brake fluid replacement schedule, follow that schedule.
Taking service work to the next level benefits both shop owners and customers.
Want to see how ALLDATA can improve tech efficiency? Check out our suite of products, each designed to contribute to both shop efficiency and productivity.
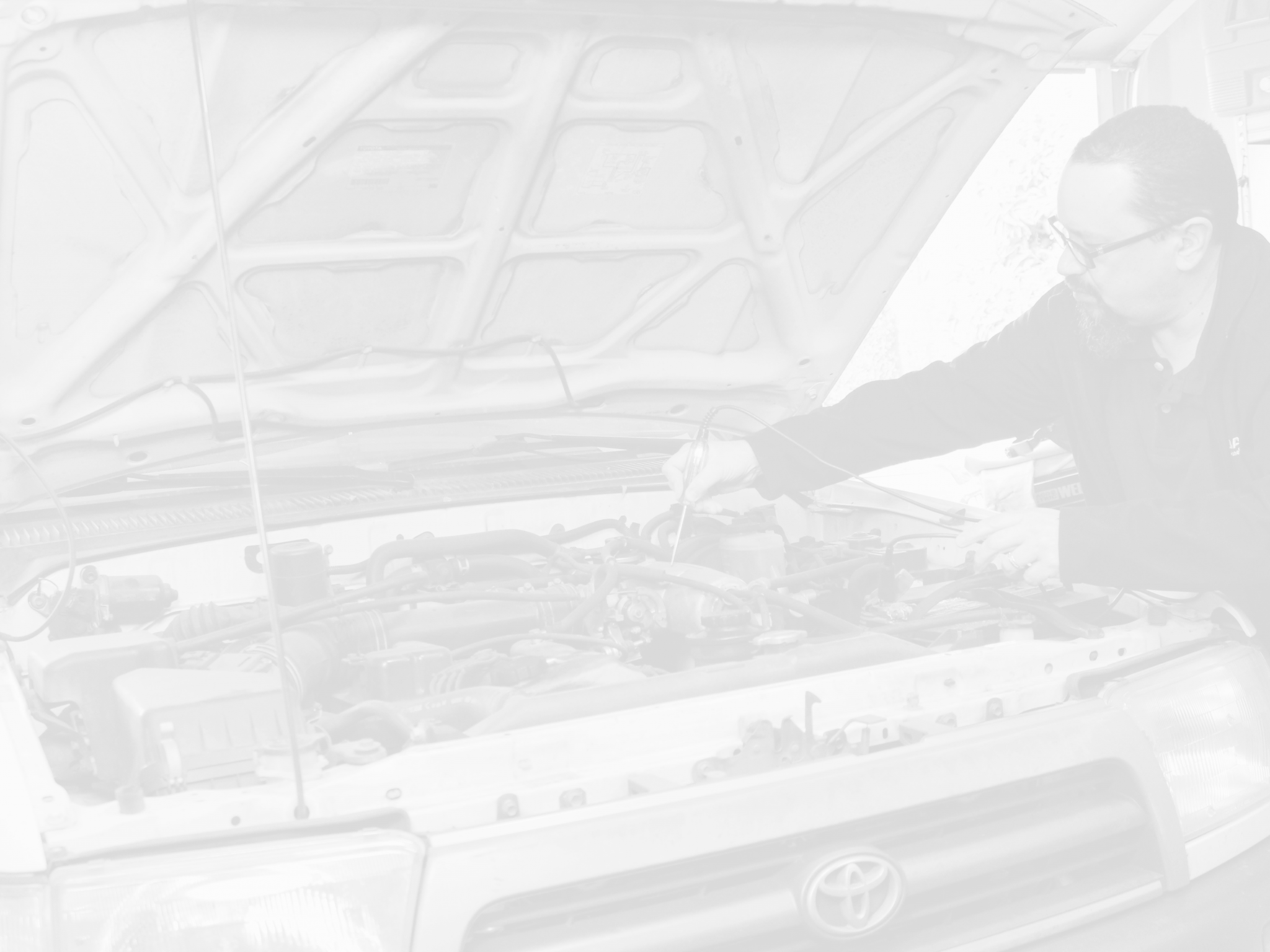