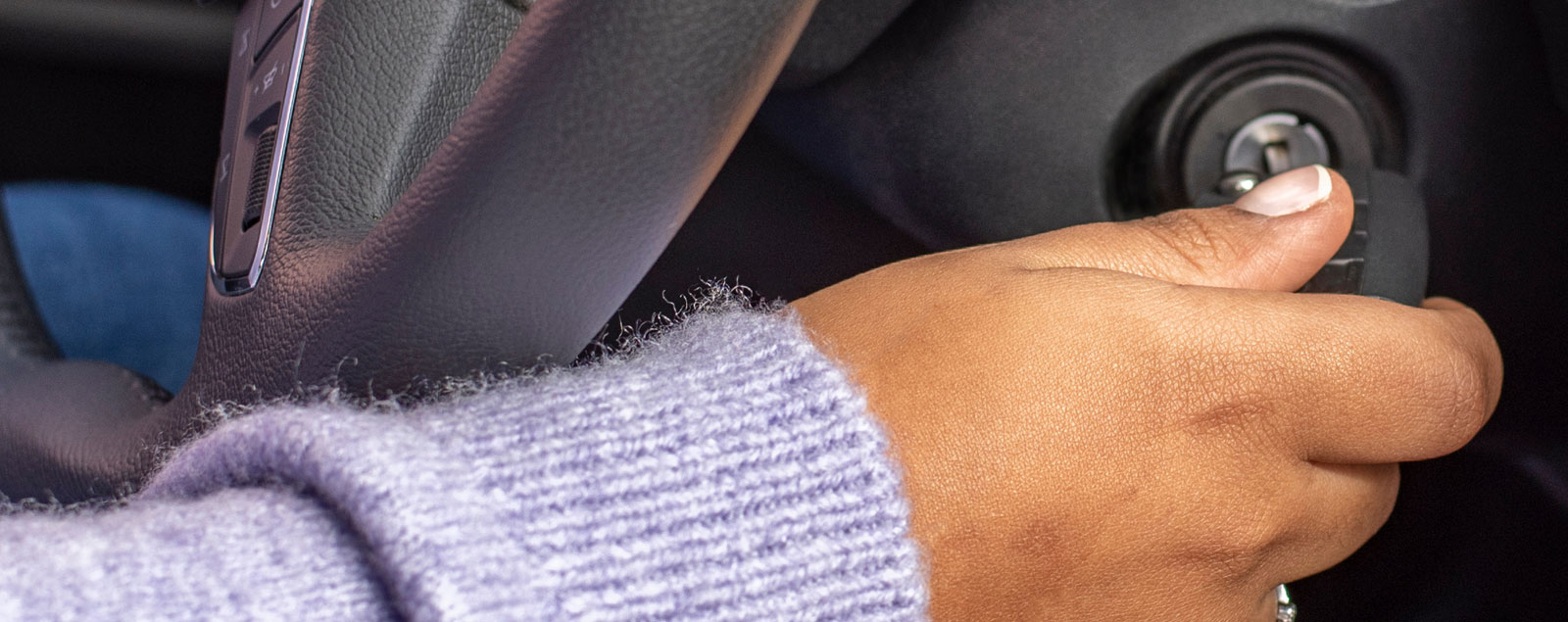
A quick start guide to no-start diagnostics
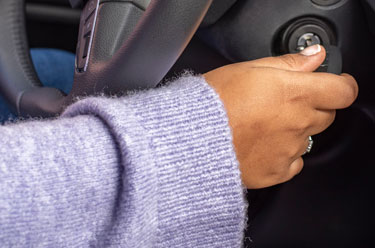
A common customer complaint is that their vehicle will crank but not start. Luckily, there are a few quick hacks designed to identify what system is affecting the starting cycle. (NOTE: This article will not cover specific test steps, but rather will outline the most efficient order in identifying what is missing in the ignition sequence.)
To start properly, the internal combustion engine needs enough compression, fuel, and spark, all happening at the right time. So let’s begin with the following two items:
Obviously, check the check engine light
The first step is to make sure the check engine light is on with the key in the run position. If it is on, you can check for codes that might indicate the problem. If it isn’t on, the computer may not be getting power or it may have a bad ground.
Don’t underestimate the cranking
Listen to the engine while cranking. Does it sound like its cranking at normal cranking speed? You can verify by watching the RPM data PID and compare it to a cranking RPM specification.
- If there is no RPM signal while cranking, then the CKP sensor is suspect and that needs to be investigated first.
- If the engine cranks too fast, it may have a broken or slipped timing belt or chain. The cylinders could also be washed down from fuel, or the engine may have worn piston rings (see below in the section on “Compression” for further information.)
- If cranking speed is too slow, then it may have a low battery, faulty cables, starter, or engine mechanical problem.
- If the cranking speed is normal, the problem is most likely centered around issues with the fuel or spark.
After establishing a basepoint on the check engine light and cranking speed, you can move on to testing systems. These hacks are designed so that the testing order should be dictated by what is easiest to access for the vehicle. You will either find the problem immediately or at least eliminate the easiest first, one possibility at a time.
Fuel
You could check the fuel gauge reading or test the fuel pressure and volume, but it is much easier to just spray fuel into the intake to see if it will run. If it runs, you know it is not getting any (or at least not enough) fuel but that it has adequate spark.
You can then check to see if the tank has fuel by taking the fuel cap off and shaking the car while listening for a sloshing sound. Then, while the key is turned to the start position (by an assistant), listen at the fuel filler inlet with the cap off for the tell-tale noise of the fuel pump. If there is fuel and the pump makes noise, then it is time to see if that fuel is making it to the injector rail using a fuel pressure gauge. Next, check the volume: 7 ounces in 10 seconds will generally be enough for any engine to start and run. You know the ignition switch, computer, fuse, and relay are all doing their jobs, but you do not know if the pump is supplying enough fuel pressure and volume.
If you don’t hear noise, have someone turn the key while you check at the pump for power and ground. Work your way back and use a wiring diagram to test where electrical power is being lost. There might be a wiring, connector, switch, or relay failure.
If there is fuel pressure at the rail, check to see if the injectors are receiving a pulsed voltage. You can disconnect an injector and plug in a noid or test light to see if the injector is being energized. If it is not, then you need to search in the repair information description to see what is required by the computer to trigger the injectors. There are some that need the CKP, some that also need the CMP, and still others that need both. You can use a scan tool to see what the data stream shows for each. If those signals exist, use a wiring diagram and check to see if the power supply fuse or fuses are okay. If not, you will need to examine and test the injectors and wiring for an opening or a short. Keep in mind, a shorted injector or shorted wiring can, and often will, damage the computer’s driver circuit.
Spark
When looking for spark, use a wide gap spark tester inline between the coil and spark plug. If the vehicle has spark plug wires, connect a spark tester between a good engine ground and a plug wire. A wider gap helps simulate the higher pressure in the combustion chamber during cranking, which is higher than when it’s just running.
While someone cranks the engine, look for good quality hot spark and a good rhythm (not just one snap). If there is no spark, see if the computer is getting the signals it needs to recognize that the engine is cranking. For spark, it is usually just the CKP or sometimes a CMP. The system description in your repair reference should have this information.
If the cranking signal is good, you need to test for power and grounds at the module/coils, as well as if the fuse(s) are good and if the computer or ignition module is providing ground to the coil primary(s). If the fuse(s) are blown or wiring melted, you will need to check the coils and wiring. Coils that are older or overheated can electrically spike internally and short out. This, in turn, will blow fuses and possibly damage the ignition module and/or computer. Wiring that is shorted to ground can sometimes burn out a coil and even occasionally a computer driver.
Compression
If the engine has good spark and is delivering enough fuel, you are finally at compression testing. These are the tests that usually take the most time.
If the engine has been receiving fuel, and the driver has tried to start it by cranking it repeatedly, you can bet there is a cylinder wash down condition. Pull the plugs and crank it to clear any residual fuel out. Then, squirt some oil in it to help seal the rings, reinstall the plugs, and try to start it.
If it still does not start, do a compression test to check the pressure reading. Usually, it takes at least 60-70 psi for a cylinder to fire at room temperature. When doing a compression test, test all the cylinders both dry and then wet (by squirting some oil down the cylinder). This will point you to a ring or valve problem.
These hacks are designed to help you prioritize where to start your ignition diagnostics. If you’re lucky, it’ll be one of the initial tests; if not, then at least you’re a few tests closer to narrowing down the possibilities.
Want to see how ALLDATA can improve shop efficiency? Check out our suite of products, each designed to contribute to both shop efficiency and productivity.
If you would like to read more articles like this one please subscribe to ALLDATA News.
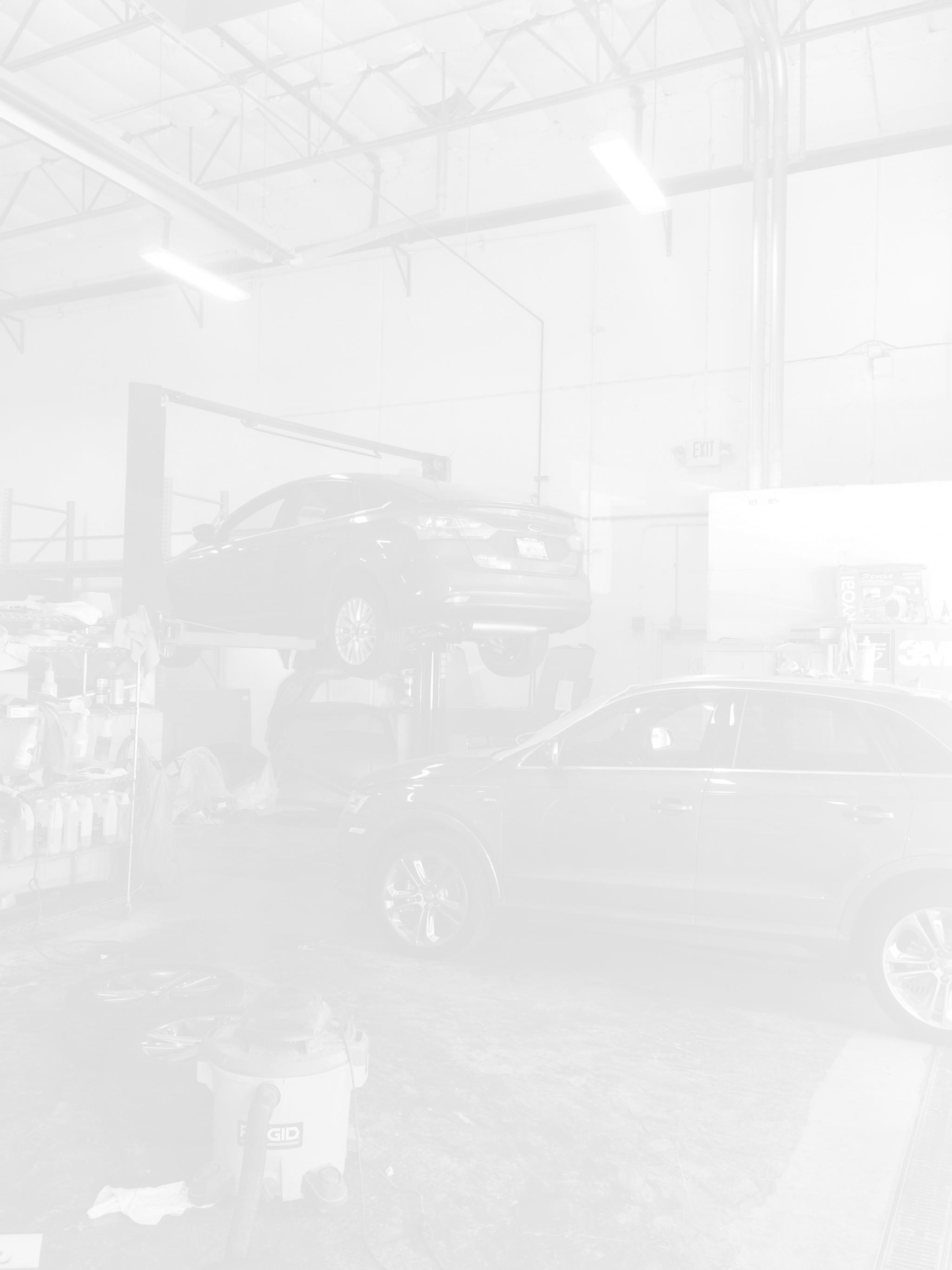